Essential maintenance tips to improve excavator uptime and resale value
By Tyler Wright, Product Manager, Operator Training, Volvo Construction Equipment
If you’re an excavator owner, operator or both, you know that a little daily TLC will help keep your machine running productively and efficiently and can increase its resale value when the time comes to trade it in.
It doesn’t take hours to inspect and maintain your excavators — a few minutes before and after your workday can make a world of difference.
It starts with a proper pre-start inspection. Just like time is money on your jobs, not taking a few minutes to do an inspection can hurt your uptime, cause unnecessary damage and wear to your machine and compromise safety.
Here are some tips to consider when performing an excavator walk-around:
- Start in the same place every day. I always start at the front of the cab. That way when I end my walk-around, I end at the cab as well and can just hop in if everything looks good.
- Make your inspection routine. Look in less obvious but critical areas.
- Look up, down, left and right. Be as thorough as possible.
- Report your findings verbally to your supervisor and provide a written version using a pre-start checklist sheet.
Pre-start checklist
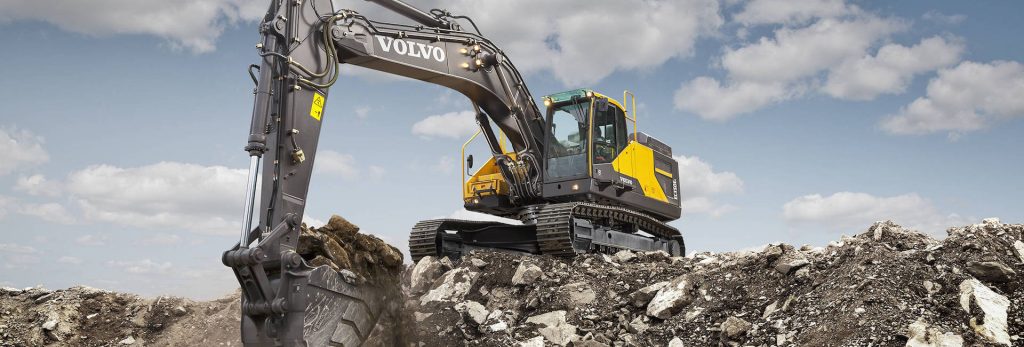
For the actual inspection, here are steps you or your crew should take each time before starting and operating an excavator:
Visually inspect all compartments to see if there’s any leakage or damage to components; then take the necessary action if anything is wrong.
Walk around the machine and conduct visual checks. Take a close look at the boom and arm for cracks, especially if you’re working in harsh conditions or in cold climates. Save time and money on unexpected repair costs by inspecting these areas:
- Boom and cylinder mounting
- Arm and cylinder mounting
- Bucket and cylinder mounting
- Main pump compartment
- Battery compartment
- Swing drive and main control valve
- Track drive
- Track chain and shoes
- Lower frame
- Superstructure
- Side doors and cowl frames
Look at the electrical box and the engine air filter. If the system indicates “full water separator,” drain it into a safe container.
Make sure the air cabin filter is clean, especially if operating in a dusty environment.
Check the radiator and coolers for any damage. If you’re working in a confined environment, ensure these parts are not clogged. A clogged cooler or radiators could result in poor performance or overheating. Be sure you’re following the maintenance intervals carefully.
- Check the hydraulic lines for leaks. A damaged line can create heat in the system or severe oil leakage.
- Check all hydraulic connections, pipes and hoses for any external damage.
- Ensure safety items like mirrors, cameras, seatbelts and the safety lever are in working order.
- Check your transmission, hydraulic and coolant fluids.
- Remove any dirt or small pieces of rock in the bucket linkage.
- Finally, turn on the main battery switch before entering the cab — no power can be distributed until the main battery switch is on.
When an excavator is new and the engine has only run for a few hours, it’s a good idea to take a look at the engine oil level. This check can be easily carried out from the cab by looking at the display. If you prefer to do it the traditional way, that’s fine too. Check the oil and always use a clean paper towel to avoid any contamination on the dipstick. The oil level should be between the minimum and maximum levels.
After your shift
There are also a few things you should do at the end of a shift to make sure the next day’s work starts off right.
Be sure to fill up with fuel at the end of the day’s shift to will reduce the risk of condensation developing in the tank overnight. While filling up the tank, fill up on diesel exhaust fluid (DEF) as well.
Always disconnect the main battery switch and park the excavator with the digging equipment fully extended. In this position, the piston rods are protected.
Clean the undercarriage to reduce strain on the components, especially during winter. If you fail to do this, mud in the chain can freeze to the undercarriage and you may be unable to move the machine the next day. Not cleaning out the undercarriage will greatly reduce its life and likely add unnecessary expenses.
Excavator undercarriage inspections
Speaking of undercarriages, they’re one of the most expensive components on your excavators to repair or replace. The undercarriage supports the total weight of the machine and is continuously subjected to rocks and other obstacles when in operation. Many of its parts are exposed to constant wear and stress.
Dealer technicians are great resources to perform undercarriage inspections, but I also recommend conducting a visual inspection once a week or every 40 operating hours, which means your technicians and operators should also be doing these.
RELATED: 6 Tips for selecting the right demolition excavator
It’s important to note that visual undercarriage inspections should not replace regularly scheduled undercarriage management. Proper undercarriage management entails measuring undercarriages, tracking wear, replacing worn components and swapping component positions to extend the total undercarriage life.
You’ll need conversion charts for each brand of undercarriage to convert them to per cent worn.
What to look for
To do an inspection on the machine, it should be somewhat clean for the sake of accuracy. Although it may be time-consuming, cleaning the undercarriage regularly will keep it in better condition, make it easier to see issues at an early stage and lessen the wear on the components.
Measure the track tension and document the results. Adjust the track tension if necessary and document the adjustments. You can find the correct track tension in your operator manual.
Remember to check these components as well:
- Track shoes
- Links
- Pins
- Bushings
- Top rollers
- Bottom rollers
- Idlers
- Sprockets
Keep in mind the sprocket is at the rear of the machine and the idler is in the front, so the right and left side aren’t mixed up in your report. Carefully check the links for cracks, spalling, side wear and wear on the pin boss. You can also count the links to see if one was removed during assembly to tighten the undercarriage. If someone has made it too tight, that will spell trouble down the road.
The last step is to compare the two sides of the undercarriage assembly. Does one side show more wear than the other? Should one side have more wear than the other?
Additional resources
If you’re unsure exactly what you’re looking at or what might need to be done to your excavator, your local dealer can help.
A telematics program is also a great way to be aware of potential issues — the best ones simplify fault codes and alerts by only sending you the most critical issues with clear information on how to resolve them (and the consequences of ignoring them).
Some OEMs even have dedicated teams that monitor telematics data for you and proactively alert you before a component fails. Buying machines with warranty coverage is another good way to ensure that your excavator components stay in good working order.
Read the full article here