Driven piles required approximately 50 percent more length than originally planned. Procuring the additional materials within the seasonal working windows was key to the successful completion of the work.
(Golden State Bridge photo)
Golden State Bridge Inc. crews began work on the replacement of the Hunter and Panther Creek bridges along U.S. 101 north of Klamath, an unincorporated community in Del Norte in northern California, in October 2020. The plan is to complete the project by next spring.
The $38 million California Department of Transportation (Caltrans) project is replacing aging structures that were built a few decades ago.
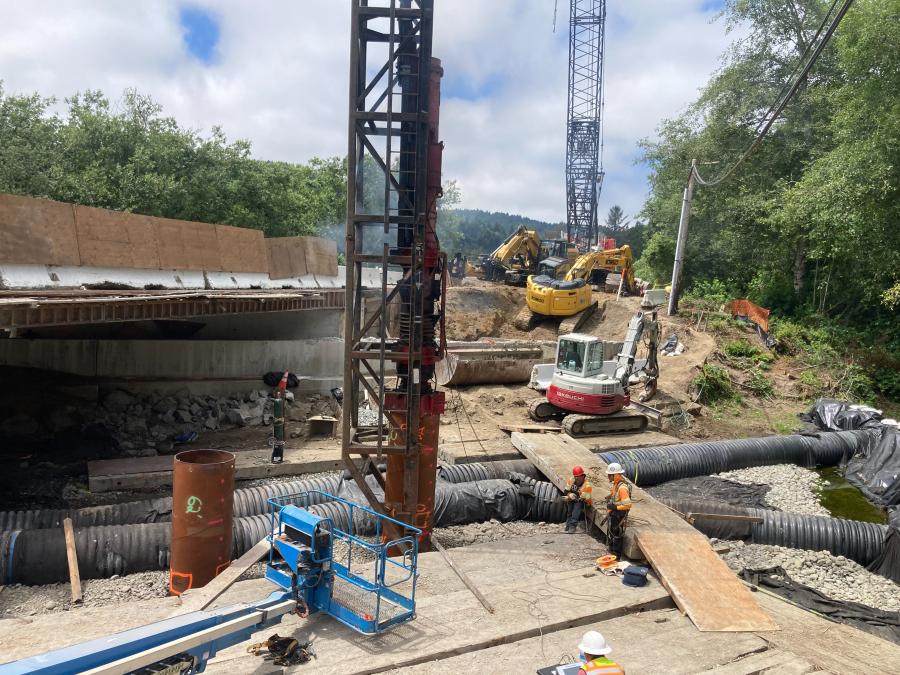
The old Hunter Creek Bridge, a concrete girder-type structure —105-ft. long and has one lane in each direction — is being replaced with a 130 -ft. long post tensioned slab-type bridge, with two x-lanes in each direction, 8-ft. shoulders on either side and a 6-ft. wide path for pedestrians and cyclists.
The old Panther Creek Bridge, a concrete girder-type structure, is 137-ft. long and has two lanes in each direction, is being replaced with a 168-ft. long steel tied arch structure-type bridge, with two lanes in each direction, 8-ft. wide shoulders on either side, and a 6-ft. wide path for pedestrians and cyclists. The new bridges are on the same alignment as the old ones.
The new Hunter Bridge is 90 percent complete, with crews focusing on roadwork and the bridge approaches to deliver it. The Panther Creek Bridge is 70 percent complete, with the remaining efforts focused on the pedestrian walkway and hanger cable assemblies.
Contractor at Work
Robert Coupe, Golden State’s project manager, is taking on the challenges successfully as the project moves forward.
“The fabrication of the components for the Panther Creek bridge occurred in several different locations by different firms,” he said. “Coordination of the components to assure proper fit was a challenge. Constant communication and coordination of shop drawings was required. Progress has been steady. Fabrication of the Panther Creek Bridge components took a long time given their unique nature and tight specifications. Fabrication was hampered by the pandemic causing production and delivery timeframes to become extended.”
The work is taking place during the day.
“At Hunter Creek, the existing ground conditions were different than anticipated,” said Coupe. “Driven piles required approximately 50 percent more in length than originally planned. Procuring the additional materials within the seasonal working windows was key to the successful completion of the work. Also at Hunter Creek, a stream diversion was installed during two consecutive seasons to allow removal of the old bridge and construction of the new bridge. At Panther Creek Bridge, an existing fiber optic cable needed to be relocated twice during the course of the work. Once to the temporary bridge and back to the permanent bridge. The utility crews worked concurrently with the bridge crews to not impact the progress of the work.
“Golden State Bridge and Caltrans have been partners throughout the duration of the project,” he added. “We have worked closely together to solve problems as they arise to keep the project moving.”
Before the reconstruction could begin, an 170-ft. long, one-lane in direction temporary bridge was built to handle local traffic.
“The temporary bridge was built in four months beginning in October 2020,” said Coupe. “The project specifications called for a contractor designed modular temporary bridge. The geometry of the bridge was depicted in the project plans [alignment, span length, etc].”
The temporary bridge is a steel truss modular bridge with asphalt paved approaches, founded on cast-In-drilled hole concrete piles and precast concrete abutments. It was assembled with a Link-Belt 80-50 hydro crane and launched with a Kobelco SK230 excavator with the cantilever supported by a Liebherr LR1250 crane.
The Hunter Bridge was demolished in two weeks, one week per-side. The Panther Bridge required one month.
“For the Hunter bridge, we demolished it in place with excavators and protective covers; and for Panther, we used cranes to hoist out entire girders and then took out the bent caps in pieces, also with cranes,” said Coupe.
Debris containment platforms were set up to capture material. Crews used a Kobelco SK230 excavator, a Liebherr LR1250 crane and a Link-Belt 238 crane.
The reconstruction of the bridges, of which the Panther Bridge has an arch, is on schedule.
The plan of attack for Panther called for the construction of abutments with precast concrete components, support steel arches from the existing bridge on falsework during erection and cast-in-place concrete decks on stay-in-place steel deck forms.
“Traffic impeded movement within the project site at times but for the most part, had no impact,” said Coupe. “Traffic was controlled with temporary traffic signals, allowing traffic to flow in one direction at a time.”
Work began on both bridges simultaneously.
“Hunter was built in two halves with traffic being moved to the completed first half to allow construction of the second half,” said Coupe. “We drove drilled 30 steel pipe piles up to 150 feet at Hunter and, for Panther, eight cast-in-drilled-hole concrete piles up to 200 feet deep. All of the fabricated items were unique to the project. Placing the pieces was not difficult, they just took a long time to get.
“Hunter was all cast-in-place concrete,” he added.. “At Panther, the precast pieces are stitched together with cast-in-place closure pours and the deck was cast-in-place. Hunter deck was completed in two pours. The Panther deck was completed in one pour, but had to have two simultaneous pours from the center of the span working outward toward the abutments. The project was in a remote location, so material supply was limited and the logistics of getting prefabbed materials to the project site was complicated.”
The Golden State management team includes Project Engineer Kyle Bommarito, Project Engineer/Project Superintendent Corey Dickens and Project Safety Manager David Blohm.
“The team dynamic is awesome,” said Coupe. “We’ve worked together for many years on different complex projects. Our crews are dedicated to producing top quality projects wherever we build them.”
Average days have 20 Golden State Bridge and up to five subcontractor employees on-site.
The amount of material generated by the demolition operations has not been finalized, although the materials are being recycled. The numbers for new materials are still being tabulated.
Golden State has one mobile mechanic that visits the site as needed.
The company owns its own equipment, purchasing pieces of iron from local and regional dealerships. CEG
Read the full article here