The total demolished building area was more than 90,000 sq. ft.
(Roadworks Construction photo)
Imagining a multimodal transportation hub in the space where an old warehouse sits might be a stretch of the imagination for residents in downtown Raleigh, N.C. But that’s exactly what regional transit authority GoTriangle is on track to accomplish for a mid-2025 opening in the Warehouse District.
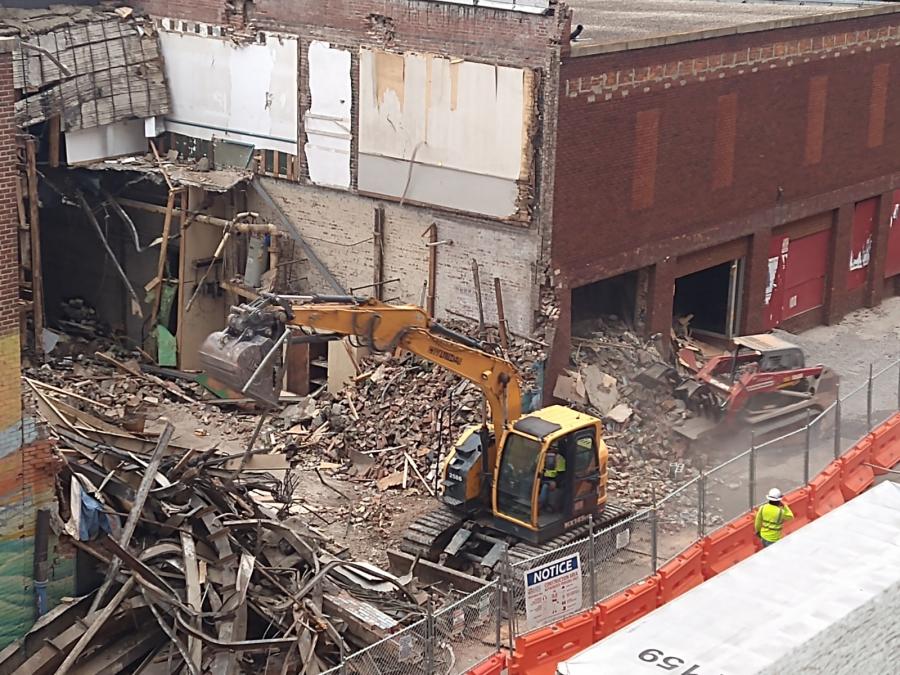
The new Raleigh Union Station Bus (RUS Bus) Facility Project will feature not just an improved and expanded transit hub for Wake County and the region but also a mixed-use development with affordable housing and private parking on a 1.76-acre site. With the population growth the area has experienced in recent years and the need of the hour being seamless connectivity, accessibility and mobility, the project is timed perfectly to serve not just local bus service but also intercity Amtrak passenger rail and bus rapid transit along with being bike- and pedestrian-friendly.
Real Estate Development firm Hoffman & Associates and architecture firm Perkins Eastman are part of the team working with GoTriangle on the project, which broke ground in spring 2022. Clancy & Theys Construction Company, a national general contractor headquartered in Raleigh, served as the general contractor for phase 1 of the project work.
The scope of work, completed during summer 2023, included oversight and coordination of project safety and subcontractors’ pre-demolition mobilization, environmental remediation, utility abandonments, building demolition, mass grading and site stabilization. Phase 1 work began with environmental remediation for removal of asbestos. This included air quality monitoring inside the existing building while asbestos was removed and properly disposed.
Safety measures included mounting water wall safety fencing around the project perimeter, which protected the boundaries of the project area along S West and W Hargett streets, and the railroad adjacent to the Raleigh Union Station. The total demolished building area was more than 90,000 sq. ft. The interior building area included existing concrete basement and first floor slabs, which spanned the entire surface area of the project.
Demolishing a building that was located close to a working railroad trackway took some creative planning to keep everyone safe, said Richard Major, GoTriangle’s director of capital development.
“For a portion of the below grade walls and footings located along the railroad, the project team figured out a way to place additional gravel-based materials to exert a surcharge on those walls,” said Major. “This method ensured that the below grade walls could withstand lateral pressures from the exterior soil, once we demolished the building walls down to grade elevation, mitigating the risk of railroad track settlement or movement. All the regional jurisdictional agencies, including the NCDOT and CSX Transportation, approved our approach, and it worked out well.”
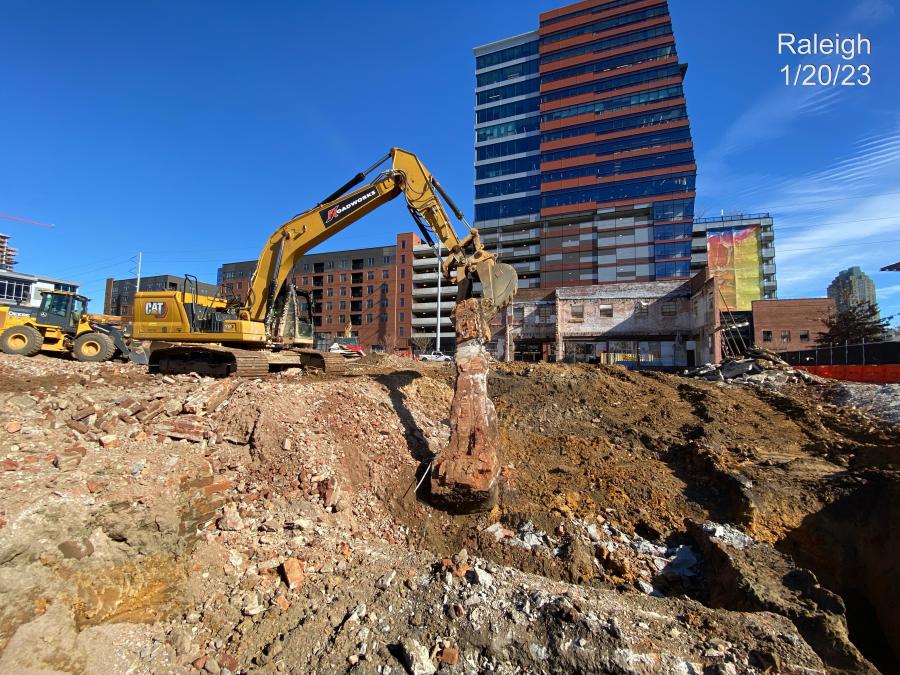
After grading the space and taking out the basement short of its original wall, the phase 1 project team found a way to save on fill materials, Major said. North Carolina-based grading and earthwork subcontractor, Roadworks Construction (DBE), worked closely with demolition subcontractor, FOSS Demolition, also North Carolina-based, to salvage as much of the concrete and brick materials as possible, for reuse as fill material.
Cement was blended with soil in some areas to help stabilize the soil. Civil engineering and design firm Stewart monitored the placement of the fill materials and quality of the soil and materials that were used. These methods resulted in a considerable cost-savings compared with having to import the full volume of fill materials as originally planned.
FOSS Demolition pulverized concrete, brick and stone into backfill material that helped provide a stable base for the foundations. With 95 percent of that process completed, approximately 5,000 cu. yds. of material needed to be imported. The project team obtained approval from the North Carolina Department of Environmental Quality, Brownfields Redevelopment Section, to import approximately the structural fill from the Lake Wheeler Assemblage Brownfields Property in Raleigh, in accordance with the project’s DEQ Environmental Management plan. This means that 11,000 of the 16,000 cu. yds. of fill material used for mass grading was borrow material originating from the project site limiting import fill. A team of 80 to 100 employees representing Clancy & Theys, FOSS Demolition, Roadworks Construction and others worked in varying shifts and stages onsite to ensure timely completion of phase 1.
With the RUS Bus Facility Project being a joint development, GoTriangle selected Hoffman & Associates to lead the development team responsible for designing and building not only the public transit facility but also the private overbuild facility that will include a more than 20-story tower now named Union West. A request for qualifications in January 2019 to identify the best private development partner with experience working on similar projects brought in Hoffmann & Associates. The firm also will provide an interim operating plan addressing safety factors for implementation when the public facility is opened for revenue operations while the highrise construction is still in progress.
Funding for the project includes a federal BUILD grant (Better Utilizing Investments to Leverage Development Transportation Discretionary Grants Program) of $20 million for costs associated with the public transit facility. GoTriangle, local and state funds will pay any additional costs for the public transit facility.
Major shared that construction of the first of three large Dillon Supply Company buildings started in the early 1900s. Construction continued in phases until the early 1970s. GoTriangle performed demolition and construction activities under the supervision of the Office of State Archaeology recording any significant artifacts discovered below grade. Additionally, portions of the existing building facade were retained in place and will be incorporated into the next phase of the vertical construction of this project.
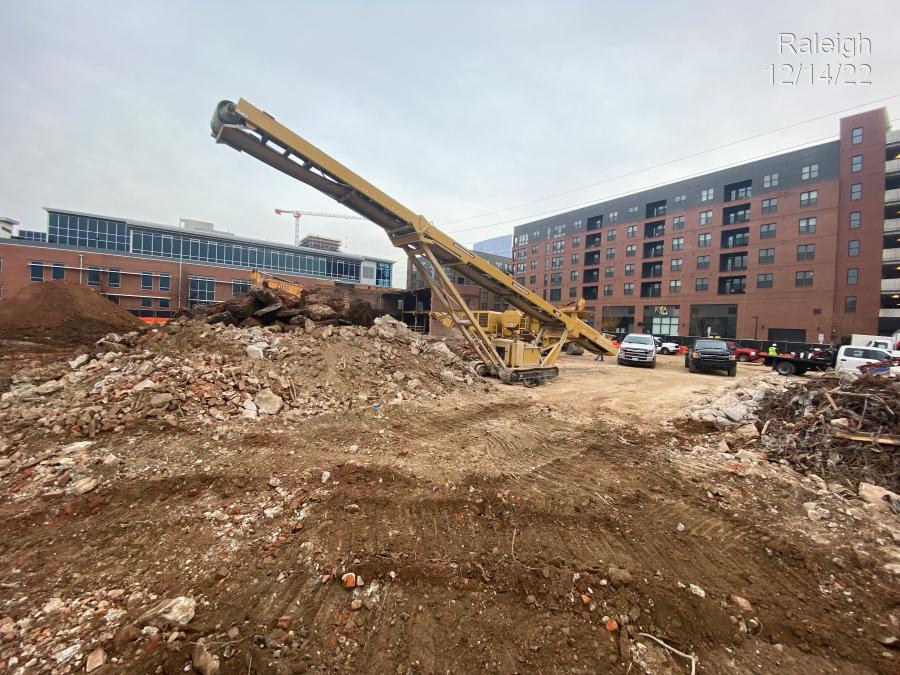
“Communication and coordination with stakeholders and partners were key to our success,” Major said. “Partnership with the city of Raleigh’s Transportation department, resulted in approval of S West Street being temporarily changed from a two-way to a one-way street, allowing construction vehicles and equipment access to the site while maintaining limited parking adjacent to businesses directly across the street. GoTriangle also partnered with Raleigh Union Station management who agreed to temporary construction access via the city plaza, and with CSX Transportation and North Carolina Department of Transportation we coordinated the use of long-reach equipment to ensure brick and concrete demolition didn’t encroach or violate nearby railroad tracks.”
Some of the specialized equipment used to complete phase 1 demolition included:
- High reach excavator: Caterpillar 330 UHD (ultra-high reach demolition excavator with a 3-piece boom and stick capable of reaching 75 ft.; used multi-processor attachment);
- Screen Machine jaw crusher: Screen Machine Industries JXT (crush/pulverize and screen concrete);
- Demolition robot: Husqvarna DXR;
- Demolition excavators: 80,000 lb. and 115,000 lb.; Caterpillar 326F and Hyundai HX145 LCR;
- Soil compactor: Caterpillar CS74B; and
- Excavator attachments: Universal and multi-processors, pulverizer and sorting grapple attachments.
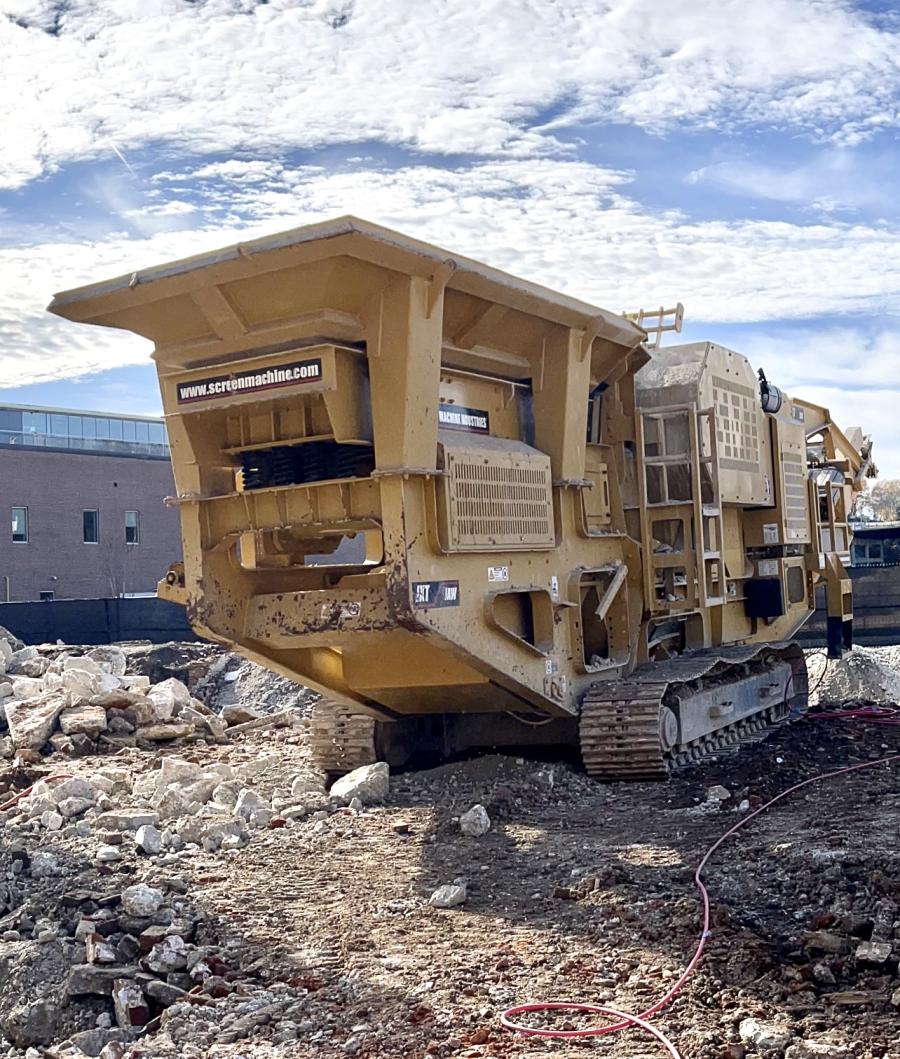
Upon completion, the overbuild’s vertical construction will be approximately a 370,000-sq.-ft. mixed-use tower and feature approximately 400 apartments with at least 10 percent affordable housing units and about 425 parking spaces. John Moriarty & Associates will be the general contractor for phase 2 construction of the joint development, with deep foundation activities planned to begin in November 2023. After Raleigh Union Station opened in 2018, the launch of this project has been highly anticipated, and progress keenly followed by residents and industry alike.
Of special significance is whether transit-integrated developments such as this provide a solution for cities with increasing populations, and therefore, an increasing need for transportation options. Peter D. Cavaluzzi, Perkins Eastman’s design principal and board director, addresses just that in a recent post for the Urban Land Institute sharing that vertically integrated transit development could be the answer to ensuring urban districts and city centers evolve into a diversity of experiences for those who live, work and play there.
To tackle the rapid growth of our cities and answer the rising demand for convenient commutes and connectivity, planning for urban spaces and the movement in and around those spaces is a process that must go hand-in-hand, affording cities the opportunity to thrive well into the future. Perhaps the RUS Bus Facility Project will provide a successful framework for other cities and urban areas to replicate. CEG
Read the full article here