Flatiron/Dragados LLC joint-venture will continue constructing the design-build, $1.2 billion U.S. 181 Harbor Bridge Project in Corpus Christi.
(Harbor Bridge photo)
The Flatiron/Dragados LLC (FDLLC) joint-venture constructing the Texas Department of Transportation’s (TxDOT) design-build, $1.2 billion U.S. 181 Harbor Bridge Project (HBP) in Corpus Christi is pressing forward and making considerable strides for an initiative that not only improves traffic flow and enhances commercial activity, but is improving life for area residents.
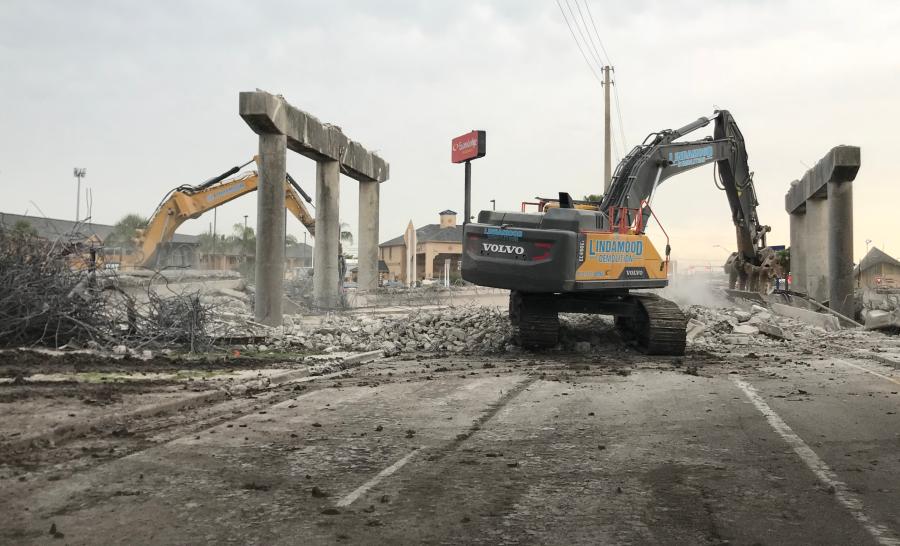
This comes after TxDOT reached an agreement with the developer of the massive construction project that settles all outstanding disputes and damage claims. With this agreement, all pending disputes between the parties have been resolved and the Notice of Default previously issued by TxDOT will be removed.
“Safety and construction excellence are the core principles of our joint venture companies and partners,” said Lynn Allison, Harbor Bridge Project public information manager. “We are grateful for this opportunity and look forward to showcasing and opening the new Harbor Bridge for the Coastal Bend community in 2025.”
The project is replacing the existing Harbor Bridge (built in 1959) with a six-lane structure that has a median barrier and shoulders, along with a 10-ft. wide shared-use path, and is reconstructing portions of U.S. 181, I-37 (1.6 mi.), and the Crosstown Expressway (1 mi.). It also includes the development, design, construction and maintenance of a total of 6.44 mi. of bridges and connecting roadways.
“Legal contract disputes for a complex project of this magnitude can be costly and drawn out,” said TxDOT Corpus Christi District Engineer Valente Olivarez Jr. “This settlement eliminates years of litigation and clears the path for work to continue to progress safely and uninterrupted on the new bridge.”
Project Construction
Before the project was temporarily paused, monthly construction reports provided updates about this immense and complex project.
“Activity on the HBP is moving at an impressive pace in 2023,” states the status report. “Transporting the massive 100-plus ton segments from our precast yard in Robstown to the approach viaducts and pylons involves significant planning.”
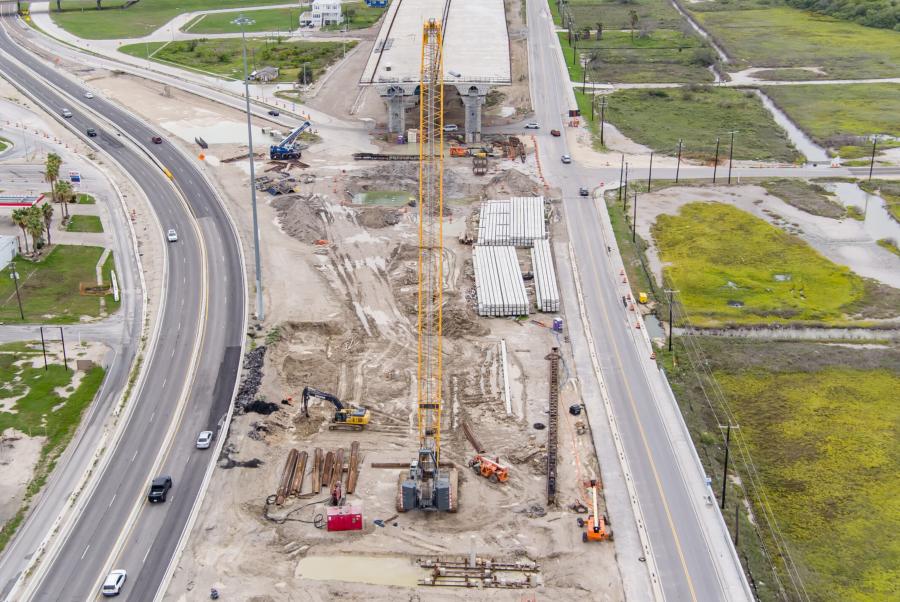
This involved mobilizing heavy cranes for loading and offloading, securing heavy load permits for transport compliance and arranging police escorts for traffic control, determining routes to factor in highway bridge clearance constraints while not impeding roadworks construction, performing earthwork to level ground before staging segments at the job site, conducting survey checks and inspections at every step to ensure the precision of each unit and sequencing the deliveries from each section of the job.
Recently, the North Approach Bridge spans were completed with the installation of the final approach segment, transported from the Pre-Cast Yard (PCY) to its permanent location on North Beach.
“The superstructure, or bridge deck, is an engineering marvel featuring 21 northbound and 21 southbound spans, each spanning 180 to 200 feet and secured with end-to-end post-tensioning,” stated the report. “Longer typical span lengths significantly reduced the number of piers required for the substructure, resulting in a less obtrusive approach bridge footprint. The NAB boasts an impressive layout with 420 northbound lane segments, each measuring 69 feet wide, to accommodate a spacious 10-foot wide shared-use path, two 10-foot wide shoulders, and three 13-foot wide mainlanes.
“The southbound lanes were also constructed with 420 segments, each 58 feet wide, providing two shoulders and three mainlanes,” it added. “These segments were cast side by side at the PCY using a premium-grade concrete mix designed for a lifespan of up to 170 years. Staggering quantities of 9,606,695 pounds of rebar and 37,360 cubic yards of concrete were utilized to fabricate the 840 NAB segments weighing 95 — 110 tons each.”
There are more than 450 workers and support personnel on-site, along with engineers and specialists. The work is closely coordinated and monitored to ensure that every step is properly constructed and that delivery of materials to individual job sites is done efficiently.
JV management team includes experienced leadership and project engineers who have worked on cable stay bridges across the world.
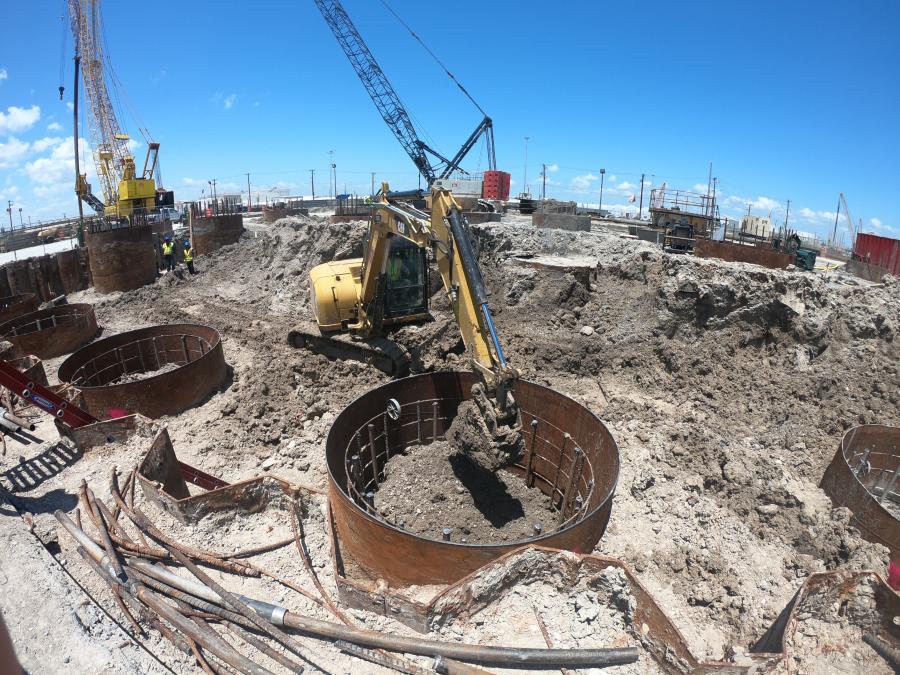
“The team is innovative and resilient,” said Allison. “The crews are dedicated and goal driven.”
Ensuring that equipment is in tip-top shape is critical and the JV has full time and rotating mechanics to ensure that repairs are done rapidly and that routine maintenance is completed on schedule.
“Wear and tear issues range from impacts of operating in a coastal environment to relocating equipment around the jobsite are addressed immediately,” said Allison. “We have a dedicated yard for mechanics to perform routine maintenance and to repair/replace parts as needed. We perform daily/monthly/annual inspections to ensure operational guidelines are followed.”
Local and regional dealerships are supporting the construction effort.
“We utilize local and regional resources when available,” said Allison. “Our team of field engineers and superintendents work closely with subcontractors and vendors to coordinate forecasted needs.” CEG
Read the full article here