The Wirtgen SP 25i with AutoPilot 2.0 paved a poured in-place concrete safety barrier between the eastbound and westbound lanes of the A 43 Autobahn near the city of Münster, Germany.
In the future, the eastbound and westbound lanes of the A 43 Autobahn near the city of Münster, Germany, will be separated by a poured in-place concrete safety barrier.
The effectiveness and permanence of such construction elements for the passive protection of road users makes them the preferred vehicle restraint system, especially on sections of roads with heavy traffic.
The monolithic profile was paved by an SP 25i using the slipform paving method. The use of AutoPilot 2.0 on this project eliminated the need for the paving crew from VSB infra GmbH & Co. KG to set up a stringline for controlling the machine.
Automatic 3D Control System Optimizes Paving Workflows
Developed by Wirtgen, the control system enables precise, stringless control of slipform pavers. It comprises a control system integrated in the machine, a base station and a tablet computer that can be used together with the Field Rover survey pole and on the slipform paver.
As the system completely eliminates the need for setting up and removing the stringline conventionally used for machine control, it also reduces the associated project times and costs. Instead of this, the machine is guided along a virtual stringline by satellite-aided navigation. This makes the entire paving workflow faster, more efficient, and, in turn, more cost-efficient. At the same time, it makes the paving of complex geometries such as tight radii or S-bends much easier, the manufacturer said.
“This is another project on which we are using stringless paving. We have been using the AutoPilot system since it came onto the market. It saves us so much time that we use it on both of our machines whenever we can,” said Kay Petersen, CEO of VSB infra GmbH & Co. KG.
More Working Space, On-Site Safety
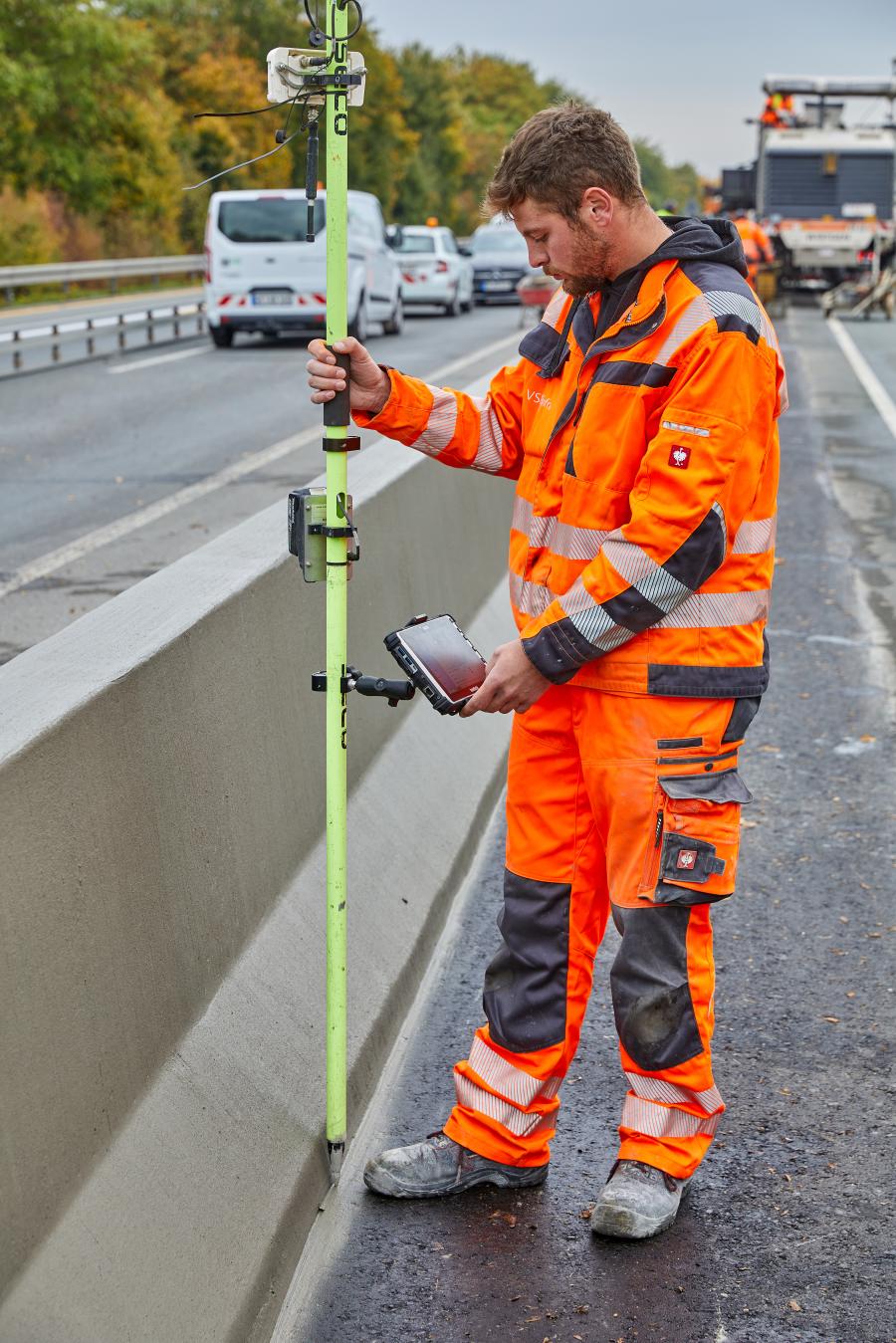
As is typical for construction sites on major highways like the A 43 Autobahn, the working area offers very little room for the paving crew. Using a stringline in front of the machine in situations like this would limit this space even more. But you won’t find one here, however hard you look. Not unless you take a look at what’s shown on the screen of the AutoPilot tablet.
The hand-held control unit displays the course of the virtual stringline and provides precise information to the machine operator at every single point along the predefined track. This also means that there is plenty of free space in front of the slipform paver.
Concrete mixers have room to maneuver and can drive right up to the paver to deliver their load. The free space in front of the machine brings the paving crew more room to work in and leads to greater safety on the project site. The absence of a stringline also removes the risk of tripping and injuries as a result of falls.
Higher Precision, Shorter Completion Times, Lower Costs
The AutoPilot 2.0 3D control system takes control of the production of all kinds of offset and inset profiles. There also is no longer any need for a surveyor to create a geodetic data model in advance. If a 3D data model already exists, this can be uploaded from the tablet and integrated in the system. Time-consuming surveys and the time and effort involved in setting up and removing stringlines are no longer required.
Planning — Implementation — Quality Assurance
The AutoPilot comes into play before the actual construction work begins. Relevant points on the project site are recorded with the Field Rover survey pole and form the basis of the digital data model for the generation of the virtual stringline on the tablet computer. This eliminates the need for an additional surveyor on the project site.
The AutoPilot then takes control of the slipform paver. The machine works its way along the predetermined virtual stringline with absolute precision. The existing sub-base of the A 43 was sampled by an ultrasonic sensor and used as a reference datum by the machine control system. The result of this is extremely precise paving of the required concrete profile.
The AutoPilot also does an important job behind the machine. The Field Rover enables extremely precise measurements of the paved profile in no time at all.
“Thanks to the Field Rover, I can perform a quality check on the paving results right behind the machine. I also really like the fact that everything comes from a single manufacturer. The machine, the AutoPilot system and the customer support,” said Site Manager Meike Teuwsen.
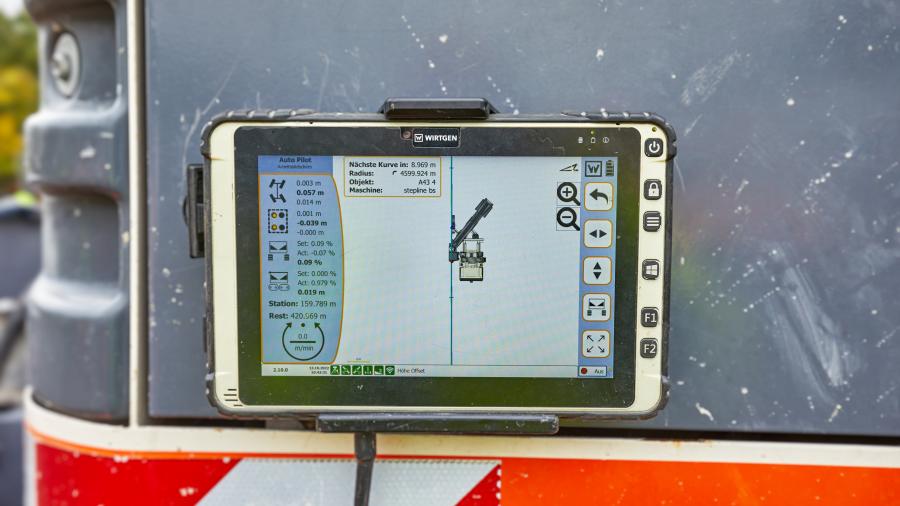
The tablet can be easily detached from the Field Rover survey pole and securely mounted on the slipform paver. The tablet screen displays all the important parameters and allows the machine operator to manually adjust the virtual stringline if and when required.
For more information, visit www.wirtgen-group.com.
Read the full article here