By Tony den Hoed, Director of Strategic Accounts — Demolition, Volvo Construction Equipment
Researching and selecting the right demolition excavator for your fleet is no simple task. I’ve shared tips for this process before in Equipment Journal, but it’s worth diving a little deeper into one specific area: factory-fitted machines versus converting a standard excavator with aftermarket options to do demolition work.
First things first: I always encourage keeping a machine’s total cost of ownership (TCO) at the front of your mind as you shop, and aftermarket versus factory-fitted decisions contribute to almost every aspect of that calculation.
Built-in protection
Let’s start with one of the most critical features for demolition excavators: guarding. This protects the cab, tracks, cylinders and other key components — increasing crew safety and reducing machine damage. A guarding package from a purpose-built demolition excavator is the best choice here because it will be designed for that specific model and remain sturdier than something that gets added on later.
It’s also a smart financial decision. Aftermarket guarding packages can cost $40,000 USD or more. They also involve working with a third party, and support could be limited. A factory-fit machine, however, should be backed by the OEM’s warranty. Another consideration is that aftermarket modifications could affect your factory warranty, so be sure to do your research.
While I’m speaking of third parties, keep in mind that the more modifications you make from different vendors, the more parties you may have to deal with should an issue arise, and I’ve seen time and again where companies blame each other for problems.
The difference a pin can make
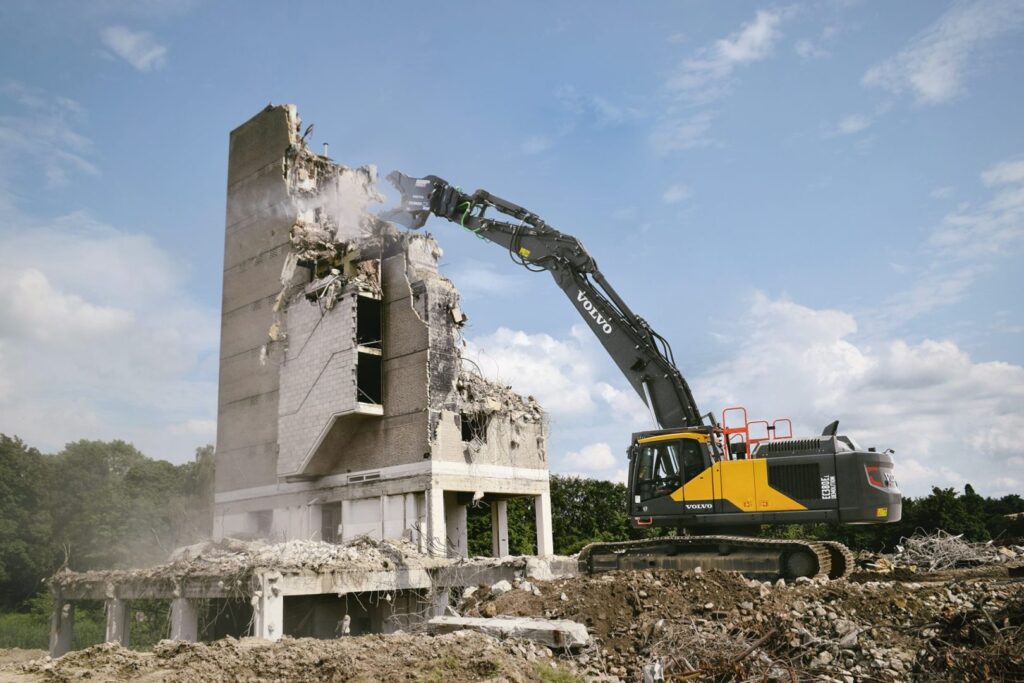
Here’s an example of how design decisions — even something as seemingly simple as a pin — can add up to a big difference. Almost every demolition excavator will have a modular joint boom concept, but the pins that hold the joint to the boom can differ. Some manufacturers and aftermarket companies use a half hook for the top pin and short pins on the bottom.
A well-designed, purpose-built demolition excavator should include full-length hydraulic pins that an operator can pull out without leaving the cab. The less an operator must leave the cab to accomplish a task, the safer and more efficient they’ll be. Also, full-length hydraulic pins are simply more reliable than short pins.
Factory-fitted means designed for the job
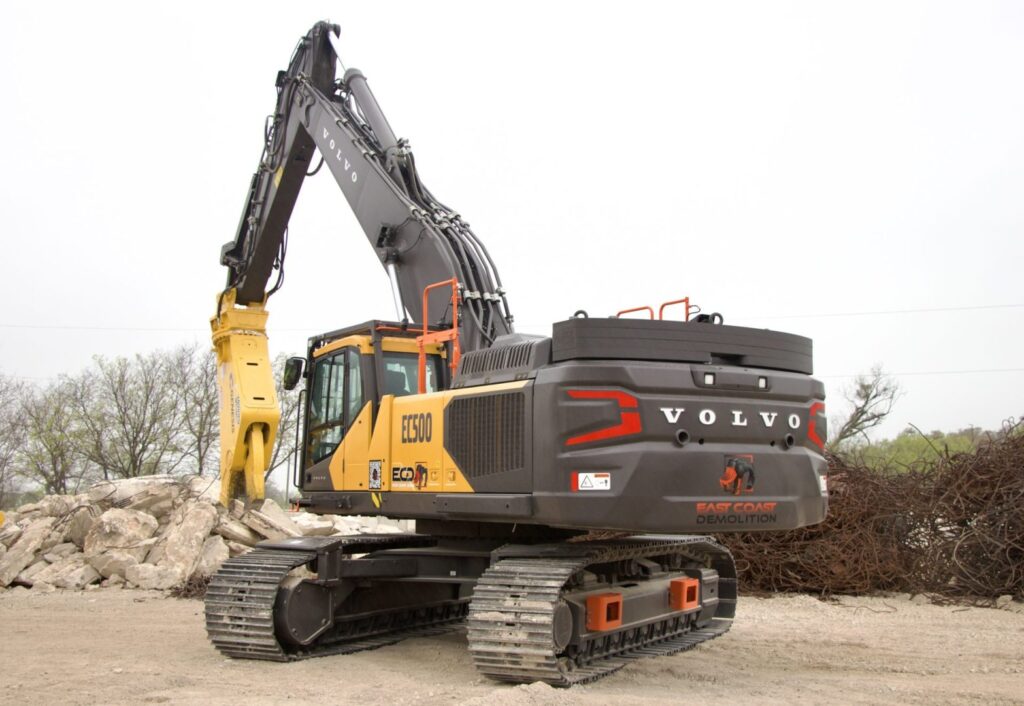
The manufacturers of a purpose-built demolition excavator will put extra thought and effort into elements that may not be as much of a focus on a standard excavator. That means larger boom cylinders, additional frame reinforcement, appropriate counterweighting, a high-visibility and demolition specific cab that tilts, a dust suppression system with pressure washer and hydraulically extendable tracks for ease of transportation and increased stability.
While some of these features can be added after the fact, they may cause a delay in getting the machine incorporated into your fleet, add more parts for your technicians to maintain or cause you to have to take it into the dealer more often, and have a bigger impact on your bottom line.
For example, you may spend $7,500 per boom cylinder, $21,000 for a counterweight, $60,000 for a tilting cab, $15,000 for a dust suppression system and $75,000 on the hydraulic extensions (All amounts are in US dollars).
The choice is clear
When jobsite safety is the number one goal, the stability, visibility, strength and intentional design of a demolition-specific excavator just can’t be matched.
Plus, there’s the expense of adding various components built by multiple manufacturers, including warranty considerations and the potential demands on your time to sort things out if there’s a claim.
Having your demolition excavator built properly from the beginning will save you a lot of time, hassle and money on top of keeping your operators and machines as safe as possible.
Read the full article here