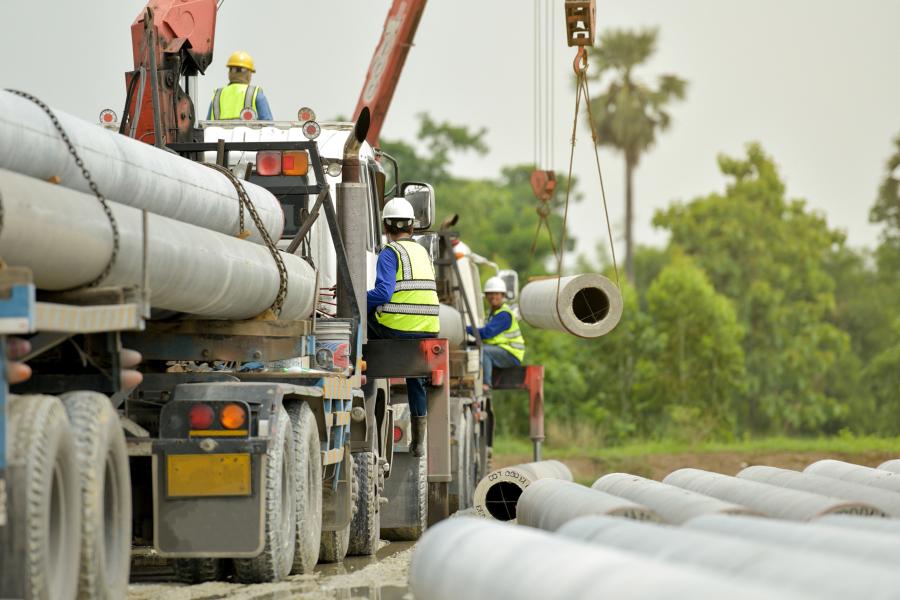
Adobe Stock photo
A comprehensive safety training program starts with the proper use of equipment, hazard recognition and emergency procedures. From there, regular safety audits should be conducted to identify potential job site hazards.
Many construction contractors are overlooking a partner in their quest for jobsite safety: their insurers. Taking advantage of safety analysis programs provided by insurance carriers can result in immediate premium discounts for fleet liability plans. However, insurers are not pushing their clients often enough to make simple changes to mitigate the safety risks on the job.
Contractors know company safety directly impacts insurance rates. Insurers assess the risk of covering contractors based on their safety practices.
“A strong safety record can lead to lower premiums,” said New York contractor GTL Construction.
A comprehensive employee safety training program should start with the proper use of equipment, hazard recognition and emergency procedures.
Regular safety audits and inspections can help identify hazards before they cause harm, said GTL.
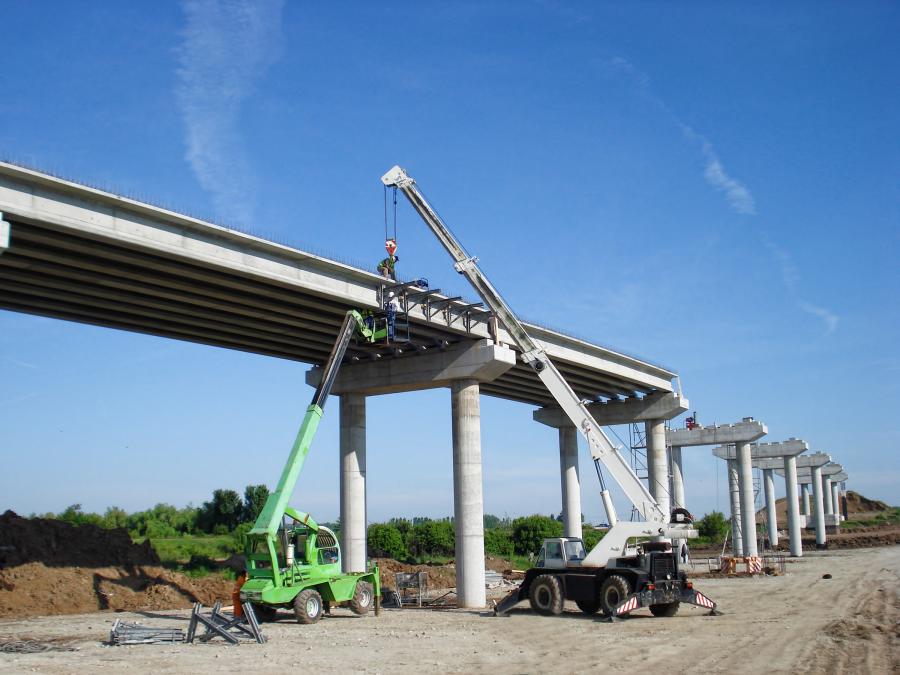
Adobe Stock photo
“By addressing these issues proactively, firms can maintain a safer work environment and demonstrate their commitment to safety to insurers.”
So can ensuring that all workers use appropriate PPE such as helmets, gloves and safety glasses.
Not only do PPEs reduce the severity of injury, but they demonstrate a proactive approach to risk management, believes GTL.
The construction company advises contractors to promoting a culture of safety. The culture should make every employee understand their role in maintaining a safe work environment that can lead to fewer accidents and injuries.
“This culture should be supported by management and include regular safety meetings and open communication about safety concerns.”
The Experience Modification Rate (EMR) is a crucial metric used by insurance companies to determine workers’ compensation premiums.
GTL explained that the rate is a numerical representation of a company’s past injury claims compared to the injury average.
An EMR of 1.0 is considered average; below 1.0 indicates a better-than-average record. And an EMR above 1.0 means a worse-than-average safety record.
The EMR is calculated over a three-year period and considers the number of claims, their severity and the industry average, said GTL in a company blog.
“The EMR directly affects the cost of workers’ compensation insurance,” according to the blog. “A lower EMR results in lower premiums, as it indicates a lower risk of future claims. Conversely, a higher EMR leads to higher premiums.”
Contractors can improve EMR by implementing robust safety programs, promptly addressing hazards and effectively managing claims.
“Reducing the frequency and severity of workplace injuries will lead to lower EMR over time,” said the construction company.
Controlling Insurance Rates
The topic of contractor-controlled insurance packages was discussed at a 2023 International Risk Management Institute conference.
These packages can be structured to produce premium discounts when fewer claims are filed, according to risk management experts.
Writing for Insurance Journal, William Rabb said insurers are hands-off a lot of the time when it comes to advising their contractor clients.
“To a large degree, workers’ compensation and commercial liability insurers leave it mostly to contractors to vet their operations for safety,” wrote Rabb.
“It’s usually not until after the fact, after something happens,” said TJ Lyons, a safety consultant who spoke at the construction risk conference
Contractors across the country are overlooking crucial changes in safety practices, said Lyons.
In fact, Rabb noted that unsafe practices in the United States contribute to approximately 2,000 construction worker fatalities each year.
Lyons believes the best way to foster safer job sites is to adopt best practices and insist on their consistent use. He thinks best practices and safer equipment should be part of any contracts between contractor and subcontractors.
Safety innovations should be built into a project at the design stage, said Lyons adding that safety folks are rarely involved at this point.
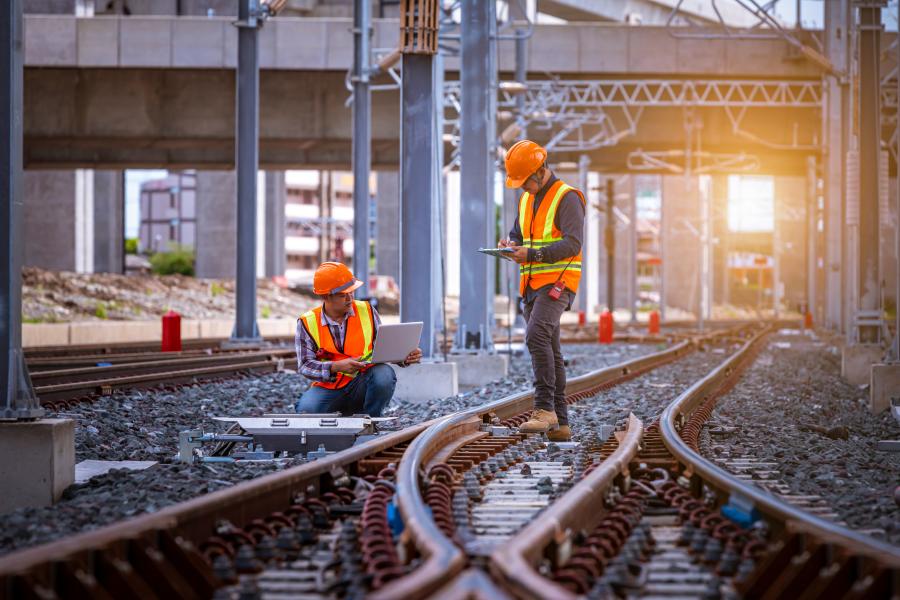
Adobe Stock photo
A strategic approach to improved safety and lower EMR needs management commitment, employee engagement and continuous improvement, believes GTL.
Start by developing a comprehensive safety program, suggests the company. “A well-structured program should include clear policies and procedures.”
A solid program also means regular training sessions and a system for reporting and addressing safety concerns.
“This program should be reviewed and updated regularly to incorporate new safety standards and best practices,” said GTL.
Involving employees can raise their commitment to a safe work environment, said GTL.
Safety committees, suggestion programs and recognition of safe behavior can engage employees.
Identify patterns and areas of needed improvement by tracking and analyzing detailed records of safety incidents. With this information, targeted interventions that reduce the risk of future incidents can be developed, said GTL.
Modern safety technology as well as effective injury management and return-to-work programs can reduce the impact of incidents on EMR.
“Investing in safety and reducing the EMR can lead to significant financial benefits for construction firms,” said GTL, offering points to keep in mind:
A lower EMR results in lower workers’ comp premiums, leading to substantial cost savings over time. Companies with strong safety records and lower insurance costs can offer more competitive bids on projects, increasing their chances of winning contracts. A safe work environment leads to higher employee morale and retention, reducing turnover costs and increasing productivity. Fewer accidents and injuries reduce the risk of legal action and regulatory fines, leading to further cost savings. A strong commitment to safety enhances a company’s reputation, making it more attractive to clients, partners, and potential employees.
American construction contractors could easily adopt safety products and best practices they’re currently overlooking, he said.
Simple steps include getting rid of ladders on construction sites. “Falls from ladders are a leading cause of serious injuries and injury claims,” said Lyons.
He believes only mechanized lifts should be used on job sites, and stilts, currently illegal in some states, should be banned for risk of injury from falls.
Safety managers and site supervisors should prevent the use of heavy equipment in blind spots.
“Some cranes and boom trucks have the lift arm at a resting position to the side of the driver compartment, blocking the lateral view,” said Lyons.
Electrical panels should readily indicate if, and when, they are energized instead of forcing a worker to open the panel to check.
Lyons said some units are designed with windows on the panel itself; other manufacturers offer light-up devices.
“Don’t use powder-activated fastener systems that contain lead,” he advised. “Put it in the contract — guns with no lead.”
With the nation’s diminishing workforce, drop-arrest hoisting systems should be used.
Better than a rope to lift heavy loads to height, drop-stop load arrestors prevent material and equipment from falling onto workers if the rope is released.
Have systems pre-assembled and delivered. Load electrical cables into conduit off-site and build rebar mats in the shop, saving time in the process, said Lyons.
Looking to Your Provider
Ask your insurer for advice on how to mitigate risk, improve EMR and reduce the cost of insurance premiums.
Many workers comp insurance companies hire third-party vendors for jobsite inspections, said Mordechai Kamenetsky of Kickstand Insurance.
Representatives can inspect a construction site for potential risks, which they then discuss with the contractor in charge of the job site.
“These loss control specialists can provide employers with recommendations regarding what changes may need to be made,” said Kamenetsky.
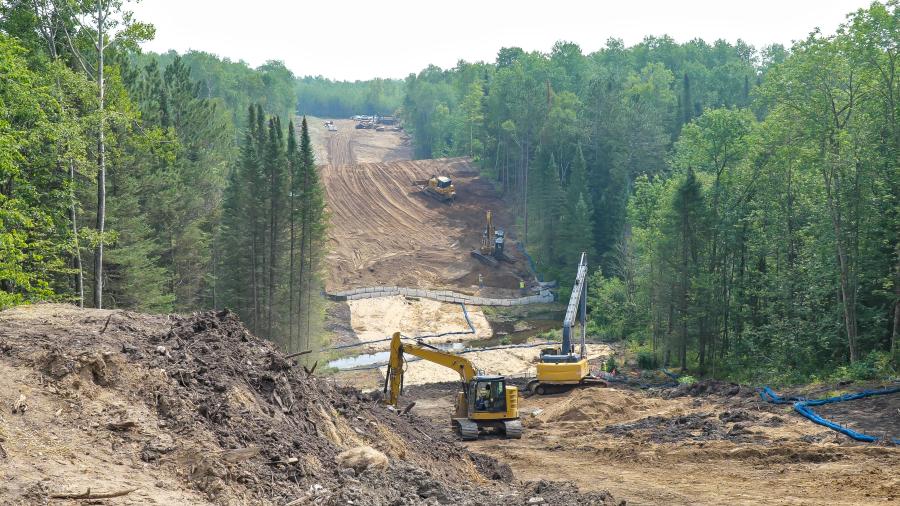
Adobe Stock photo
In fact, insurers may require certain actions be taken to reduce risk after the loss control inspection is completed, he said.
“Typically, they are going to look for potential issues that could cause harm to workers [and] end up causing workers’ compensation claims in the future.”
You can ask your insurer to work with you by providing you with a list of best practices to follow. The goal is to reduce claims in the future.
Site visits and loss control surveys are often required by insurance companies as a part of your workers’ compensation policy.
“Those who are happy with their current insurer should strive to make any changes discussed with the inspector,” said Kamenetsky.
He urges contractors not to ignore calls from loss control inspectors. It can be a “huge” mistake.
“It will make it appear to your insurance company that you aren’t willing to go through the inspection and make changes,” he said. “Remember, their recommendations are not usually a suggestion. They need to be adhered to if you hope to keep your current workers’ compensation policy.”
If you ignore the calls and e-mails the inspector will be forced to report to the insurer your failure to comply with policy — considered grounds for cancellation.
“Although some businesses might feel that insurance companies are overstepping … it’s important to remember that it benefits everyone,” said Kamenetsky.
Business owners don’t want workers injured and insurers don’t want to pay out claims if there are preventable measures that can be taken instead.
He said in some instances, insurance companies might even offer incentives to businesses that take certain actions to reduce risk.
If a business is deemed high-risk for some reason and they don’t remedy the issues, the insurer could increase the cost of the policy or not offer a policy at all.
“Of course, you will also find that loss control inspections end up being good for the employees, as well,” Kamenetsky said.
Working with your insurer by complying with inspections can help to ensure your company is taking action to make the workplace safer, he said.
“This cuts down on injuries, time out of work and claims. Everyone will benefit.” CEG
Lucy Perry
Lucy Perry has 30 years of experience covering the U.S. construction industry. She has served as Editor of paving and lifting magazines, and has created content for many national and international construction trade publications. A native of Baton Rouge, Louisiana, she has a Journalism degree from Louisiana State University, and is an avid fan of all LSU sports. She resides in Kansas City, Missouri, with her husband, who has turned her into a major fan of the NFL Kansas City Chiefs. When she’s not chasing after Lucy, their dachshund, Lucy likes to create mixed-media art.
Read the full article here