Photo courtesy of Lippmann
Updated jaw pin is included on all future Lippmann models and can be retrofitted on most current models in the field.
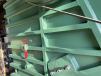

Lippmann, a manufacturer of aggregate processing equipment, announced its newly enhanced jaw safety pin.
Underscoring the company’s dedication to advancing workplace safety, the pin is designed to lock the pitman securely in the forward position during maintenance or repair and is now available for retrofit on select existing jaw models and comes standard on future jaw crushers.
The jaw safety pin is designed to prevent accidental pitman movement, a critical safety feature during servicing. With features such as a pinned locking mechanism and vertical storage location to prevent damage, Lippmann’s latest design aims to enhance safety while offering ease of use.
“We’ve prioritized safety in all our designs, and the jaw safety pin is no exception,” said Danny McElchar, director of engineering of Lippmann. “While safety pins exist on other jaw crushers, we’ve responded quickly to customer feedback to make this feature available not just for future models, but as a retrofit kit for existing customers as well.”
The updated design includes a new hole on each side of the jaw box, a boss and a brace added to the jaw box rib. Some models also will incorporate a modified cheek plate or side liner to accommodate the new locking pin system, which allows for safe pitman positioning during service. Additionally, decals provide clear instructions on proper usage of the pin, ensuring operators are aware of the safety features.
For more information, visit Lippmann-Milwaukee.com.
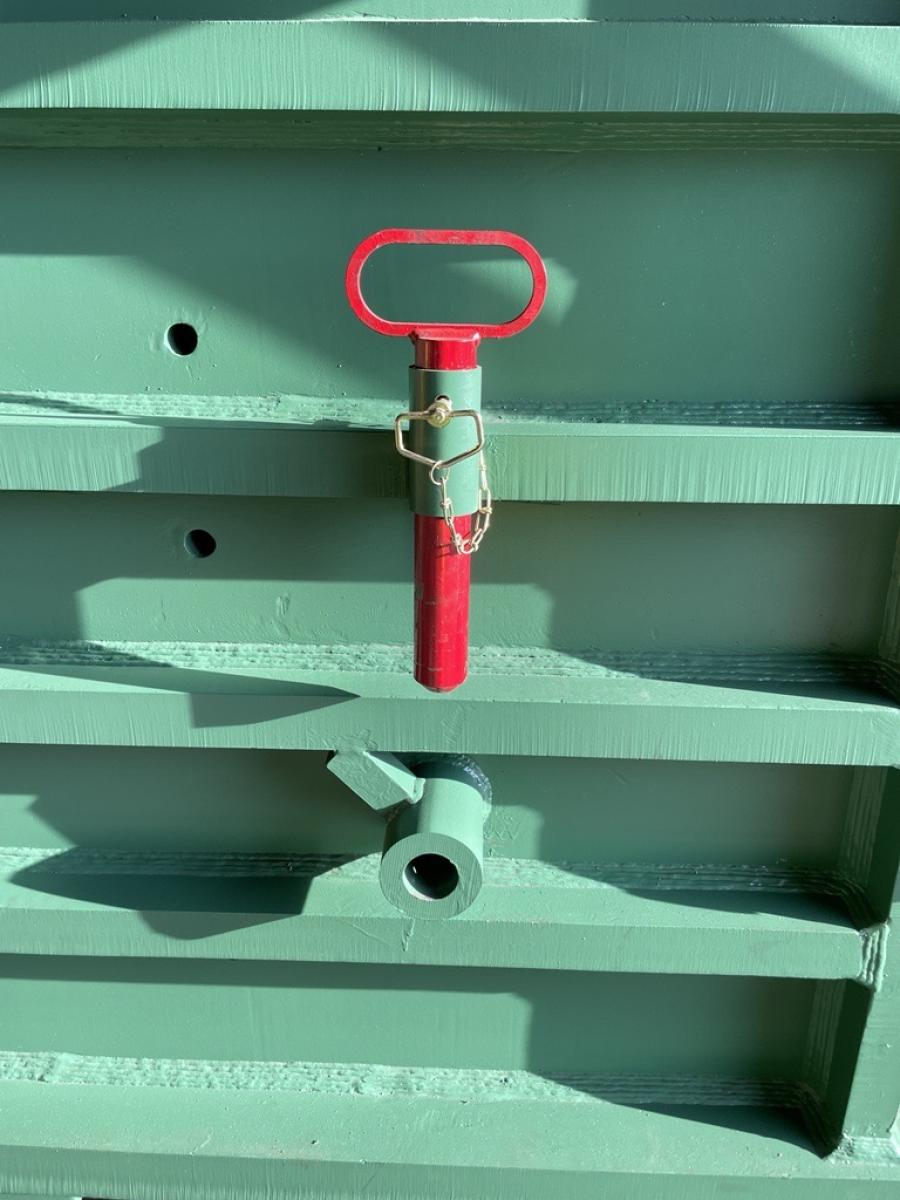
Photo courtesy of Lippmann
Lippmann’s new jaw pin focuses on safety, preventing movement of the pitman during maintenance.
This story also appears on Aggregate Equipment Guide.
Read the full article here