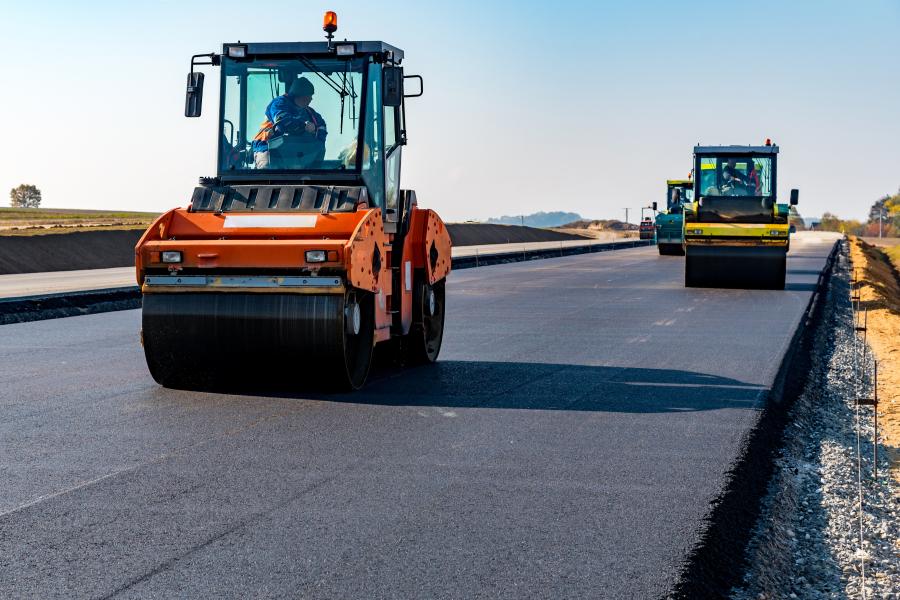
Adobe Stock photo
The increased cost of construction is tapping more dollars from the bipartisan infrastructure bill, reducing the amount of infrastructure that can be bought today.
Rising highway construction costs are draining more dollars from BIL funds allocated for federal transportation projects across the country. The FHWA admits that what can be purchased today with BIL funds earmarked in 2021 is markedly less that what was pledged. Those construction costs rose an “unprecedented” 26 percent in 2022. The record annual increase was 20 percent in 2005, said the agency.
Tracking numbers, the DOT Bureau of Transportation Statistics (BTS) found that from the first quarter of 2022 to 2023 costs rose 35 percent.
It reduces “the amount of highway infrastructure that can be bought today versus what could have been purchased prior to the price increases.”
The agency put it another way: “The same construction project today costs more than yesterday and significantly more than in 2021.”
Analyzing the Situation
The AGC noted that prices for construction inputs have risen faster than contractors’ bids every month so far in 2024.
“Persistently long lead times for electrical equipment are adding to the cost of building and infrastructure projects,” said Ken Simonson, chief economist. “Meanwhile, inflexible rules for sourcing materials could drive up prices for federally aided projects such as highways.”
The AGC partnered with ARTBA on a survey tracking the impacts on highway construction of proposed tighter Buy America requirements.
Some 69 percent of respondents said they’d “price” their bids to register uncertainty about costs of Buy America-compliant materials for particular projects.
“This reality usually results in higher project costs and diluted benefits from federal investment,” said Simonson. “In addition, if FHWA rolls back its waiver, respondents expect significant challenges in complying with Buy America requirements for many manufactured products.”
Adobe Stock photo
Less than 15 percent of respondents believe these products would be easy or possible to acquire in compliance with the Buy America policy.
Survey respondents listed numerous additional products that would be difficult or impossible to source without waivers.
“Federal officials are attempting to shut down a diversified global supply chain … before enough domestic supply exists,” said Jeffrey D. Shoaf, CEO of the AGC. “That’s a recipe for higher costs and delayed projects that will harm both the U.S. economy and highway safety.”
The BTS warned that if highway construction costs rise above their level at BIL signing, what can be bought with the funds in each fiscal year will decline.
The bureau looked at both High and Modest Inflation Scenarios in predicting what happens in the future. The High Inflation Scenario assumes construction costs continue to rise at their current rate using the average annual growth from 2021 and 2022.
“Under this scenario, only $224.2 billion can be bought with the $379.3 billion allotted for highways,” said BTS. “In other words, only 60 percent of what could have been bought … when BIL was signed can be bought over the five years from 2022 through 2026.”
The agency noted that situation represents a whopping 40 percent reduction.
The Modest Inflation Scenario assumes a more modest growth in construction costs equal to the average annual growth in 2019 and 2021.
“Under this more modest growth scenario, $260.5 billion can be bought with the $379.3 billion allocated … due to increased highway construction costs.”
This amount is 16 percent more than what could be bought if highway construction costs continue to rise at their current higher rate, said BTS.
But it’s still only 69 percent of what could have been bought when BIL was signed.
“In other words, a 31 percent reduction in what could have been constructed in 2021 when highway construction cost less.”
Materials prices are to blame for a lot of the headaches the construction industry faces with BIL projects. The bureau tracked increases in crude oil used to produce asphalt, which it said contributed to the situation. In fact, BTS reports U.S. crude oil increased 594 percent, from $16.55 per barrel in April 2020 to $114.84 per barrel in June 2022.
That’s the second highest price on record and makes asphalt a top contributor to increases in the National Highway Construction Cost Index (NHCCI).
These numbers are from the last quarter of 2021 through the third quarter of 2022.
“Crude oil prices have fallen since the June 2022 high but have risen steadily since the beginning of 2024,” said BTS.
The bureau said that situation suggests construction costs may rise further in the future.
Supply-chain issues, which began in 2020 with COVID, are also contributing to the hike in the cost of highway construction.
The pandemic caused both temporary and permanent business closures. It also increased demand for durable goods.
“This, in turn, caused material prices to rise,” said the bureau. An increase in the producer price index (PPI) for all goods and services shows just how.
The PPI grew by 51 percent from April 2020, the lowest point since May 2016, to a new all-time high in June 2022, said BTS.
The NHCCI actually fell a half a percentage point from October to December of 2023, according to FHWA’s quarterly index.
Jeff Davis of thinktank Eno said that using the new NHCCI seasonal adjustment, the final quarter 2023 was still 4 percent above the previous period.
FHWA economists said, “there is a historically negative seasonal effect during Q4 and Q1 that may be contributing to the slight deflation.”
Adobe Stock photo
It’s visible on FHWA’s line chart of the NHCCI going back to its inception in 2003, said Eno.
The original index divots downwards in the fourth quarter of many years, as cold weather curbs construction activity and demand for materials.
“However, when you add it all together, year upon year, there is no real cumulative difference in the old rate vs the seasonally adjusted rate,” said Davis.
In both instances, the cumulative increase in highway construction costs since the October-December 2020 quarter is 68 percent.
“Converting this to actual dollars lost … the FHWA has signed $182.4 billion in contracts and other spending obligations since January 1, 2021,” added Davis.
Once the nominal dollars convert to “real” at the October-December 2020 quarterly NHCCI, that $182.4 billion drops down to $132.9 billion.
That means “that $49.4 billion has been lost to highway cost inflation since January 2021,” Davis said.
But, he added, even the nominal numbers reveal something interesting about FHWA and state DOTs.
The two signed a smaller dollar amount of contracts in the last two quarters of 2023 than in the last four quarters of 2022.
“This may be linked to the ongoing August Redistribution crisis,” said Davis.
He believes some states may be running out of ready-to-go highway projects that can be put out to bid and started quickly.
Adding to Cost of Construction
Federal mandates pushing contractors to hire union labor is “the worst way to do infrastructure projects,” said Ben Brubeck of ABC.
“Taxpayers lose when responsible contractors that do a quality job at the best price are frozen out,” Brubeck wrote for the media outlet Governing.
He said the construction industry’s “perfect storm” of workforce shortage, materials price inflation and controversial public policy is to blame.
It’s “undermining hundreds of billions of dollars of taxpayer investments in federal, state and local government infrastructure projects.”
Brubeck said it’s also hurting clean energy and manufacturing projects procured by private developers.
“This means fewer improvements to roads, schools, water systems and energy infrastructure and fewer well-paying construction jobs.”
He cited President Biden’s Buy America laws, project permitting regulations, workforce development and labor policies as well as the failure to reduce costly red tape.
Adobe Stock photo
Combined, the issues are “diminishing the value hard-working taxpayers deserve from investing in America’s infrastructure projects,” said Brubeck.
And he called Biden’s mandatory project labor agreements for contracts of $35 million or more “one of the most controversial Biden administration policies.”
Brubeck said the policy excludes nearly 90 percent of the construction workforce “and some of the best contractors in the industry” from competing.
The project-specific collective bargaining pacts are designed to steer taxpayer-funded contracts to unionized contractors and union labor.
“Government-mandated PLAs needlessly exacerbate the construction industry’s skilled labor shortage,” said Brubeck.
They force the replacement of existing employees with workers from specific union halls and the adoption of “inefficient” union work rules, he said.
The result is excessive cost burdens and safety and quality risks for high-performing non-union contractors who can’t compete for taxpayer-funded projects.
“Non-union firms employ a historically high 89.3 percent of the U.S. construction industry,” said Brubeck, ABC vice president of regulatory affairs. “Quality and experienced non-union contractors have built more than half of large-scale federal construction projects since 2009.”
These non-union contractors also are more likely to be owned by women and minorities, he added, and research has found PLA mandates increase construction costs by 12 to 20 percent, he said.
That means voters can expect fewer improvements to important local infrastructure projects — and fewer jobs, Brubeck believes.
“This administration’s effort to freeze the majority of experienced contractors … out of competing is sure to create delays and needless infrastructure inflation.”
On the bright side, Brubeck said builders are fighting back. In fact, ABC filed suit against the PLAs mandate on federal projects.
The organization said Americans deserve long-lasting construction projects built safely, on time and on budget by the best contractors and workers regardless of labor affiliation.
Lawmakers, governors and industry are urging Congress to stop inflationary PLAs by passing the Fair and Open Competition Act, said Brubeck.
The act would prohibit PLAs on federal and federally assisted construction projects, he said.
“All Americans would be best served by inclusive, win-win policies that help provide a cost-effective return on federal investment in infrastructure.” CEG
Lucy Perry
Lucy Perry has 30 years of experience covering the U.S. construction industry. She has served as Editor of paving and lifting magazines, and has created content for many national and international construction trade publications. A native of Baton Rouge, Louisiana, she has a Journalism degree from Louisiana State University, and is an avid fan of all LSU sports. She resides in Kansas City, Missouri, with her husband, who has turned her into a major fan of the NFL Kansas City Chiefs. When she’s not chasing after Lucy, their dachshund, Lucy likes to create mixed-media art.
Read the full article here